Brushlike arrays of electrodes packaged with application-specific integrated circuits (ASICs) are undergoing development for use as electronic implants — especially as neuro-prosthetic devices that might be implanted in brains to detect weak electrical signals generated by neurons. These implants partly resemble the ones reported in “Integrated Electrode Arrays for Neuro-Prosthetic Implants” (NPO-21198), NASA Tech Briefs, Vol. 27, No. 2 (February 2003), page 48. The basic idea underlying both the present and previously reported implants is that the electrodes would pick up signals from neurons and the ASICs would amplify and otherwise preprocess the signals for monitoring by external equipment.
The figure presents a simplified and partly schematic view of an implant according to the present concept. Whereas the electrodes in an implant according to the previously reported concept would be microscopic wires, the electrodes according to the present concept are in the form of microscopic needles. An even more important difference would be that, unlike the previously reported concept, the present concept calls for the inclusion of microelectromechanical actuators for adjusting the depth of penetration of the electrodes into brain tissue.
The prototype implant now under construction includes an array of 100 electrodes and corresponding array of electrode contact pads formed on opposite faces of a plate fabricated by techniques that are established in the art of microelectromechanical systems (MEMS). A mixed-signal ASIC under construction at the time of reporting the information for this article will include 100 analog amplifier channels (one amplifier per electrode). On one face of the mixed-signal ASIC there will be a solder-bump/micropad array that will have the same pitch as that of the electrode array, and that will be used to make the electrical and mechanical connections between the electrode array and the ASIC. Once the electrode array and the ASIC are soldered together, the remaining empty space between them will be filled with a biocompatible epoxy, the remaining exposed portions of the ASIC will be covered with micromachined plates for protection against corrosive bodily fluids, and then the ASIC and its covering micromachined plates will be coated with parylene.
The implant includes a top plate, into which through-holes of the same pitch as that of the electrodes have been micromachined. The plate is mounted so that the electrodes protrude through the holes. The implant also includes a bottom plate without through-holes. The depth of penetration of the electrodes into brain tissue (more precisely, the thickness of, and the length of protrusion of the electrodes from, the implant package) would be controlled by use of microelectromechanical actuators that would move the top and bottom plates toward or away from the MEMS electrode-supporting plate.
The microelectromechanical actuators would be controlled by electrical signals from the ASIC. According to one concept under consideration at press time, the actuators could be microfabricated electrochemical cells containing solid electrolytes that expand by large amounts (increase in thickness of the order of 50 percent) when charged to potentials of the order of 3 V. The control signals for the transducers could originate in external equipment or could be generated by an on-chip servocontrol subsystem that would strive to adjust the depth of penetration to maximize the strength of signals picked up by the electrodes. The ASIC will include a section for induction and/or radio reception of power and control signals from, and for transmission of electrode readout signals to, external equipment. A simple wire dipole antenna or a printed spiral coil on a flexible substrate could be used to couple the signals between the implant and external equipment, without need for wire connections.
This work was done by Jay Whitacre, Linda Y. Del Castillo, Mohammad Mojarradi, Travis Johnson, William West, and Richard Andersen of Caltech for NASA’s Jet Propulsion Laboratory. For further information, access the Technical Support Package (TSP) free online at www.techbriefs.com/tsp under the Bio-Medical category.
In accordance with Public Law 96-517, the contractor has elected to retain title to this invention. Inquiries concerning rights for its commercial use should be addressed to:
Innovative Technology Assets Management
JPL
Mail Stop 202-233
4800 Oak Grove Drive
Pasadena, CA 91109-8099
(818) 354-2240
E-mail: This email address is being protected from spambots. You need JavaScript enabled to view it.
Refer to NPO-30516, volume and number of this NASA Tech Briefs issue, and the page number.
This Brief includes a Technical Support Package (TSP).
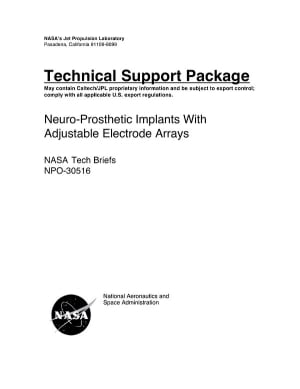
Neuro-Prosthetic Implants With Adjustable Electrode Arrays
(reference NPO-30516) is currently available for download from the TSP library.
Don't have an account? Sign up here.